Destylator przemysłowy to urządzenie, które odgrywa kluczową rolę w procesach separacji cieczy na podstawie różnic w temperaturze wrzenia. W przemyśle chemicznym, petrochemicznym oraz spożywczym, destylacja jest niezbędnym procesem do uzyskiwania czystych substancji. Proces ten polega na podgrzewaniu cieczy do momentu jej wrzenia, a następnie skraplaniu pary, co pozwala na oddzielenie składników o różnych temperaturach wrzenia. W przypadku destylatorów przemysłowych, często stosuje się kolumny destylacyjne, które zwiększają efektywność procesu poprzez wielokrotne skraplanie i parowanie. Dzięki temu można uzyskać wysokiej czystości produkty, takie jak alkohole, oleje czy rozpuszczalniki. Zastosowanie destylatorów przemysłowych jest szerokie i obejmuje produkcję alkoholu etylowego, oczyszczanie wody oraz odzyskiwanie rozpuszczalników.
Jakie są rodzaje destylatorów przemysłowych i ich funkcje
W przemyśle istnieje wiele rodzajów destylatorów przemysłowych, z których każdy ma swoje specyficzne zastosowania i funkcje. Najpopularniejsze z nich to destylatory prostego przepływu, kolumnowe oraz frakcyjne. Destylatory prostego przepływu są najprostsze w budowie i stosowane głównie do separacji substancji o znacznie różniących się temperaturach wrzenia. Z kolei destylatory kolumnowe charakteryzują się bardziej skomplikowaną konstrukcją, która umożliwia wielokrotne skraplanie pary w celu uzyskania wyższej czystości produktu końcowego. Destylatory frakcyjne są wykorzystywane w przypadkach, gdy składniki mają zbliżone temperatury wrzenia; dzięki specjalnym kolumnom frakcyjnym możliwe jest efektywne oddzielanie tych substancji. Innym rodzajem są destylatory próżniowe, które działają w obniżonym ciśnieniu, co pozwala na destylację substancji w niższych temperaturach, minimalizując ryzyko ich degradacji.
Jakie są zalety stosowania destylatorów przemysłowych w produkcji
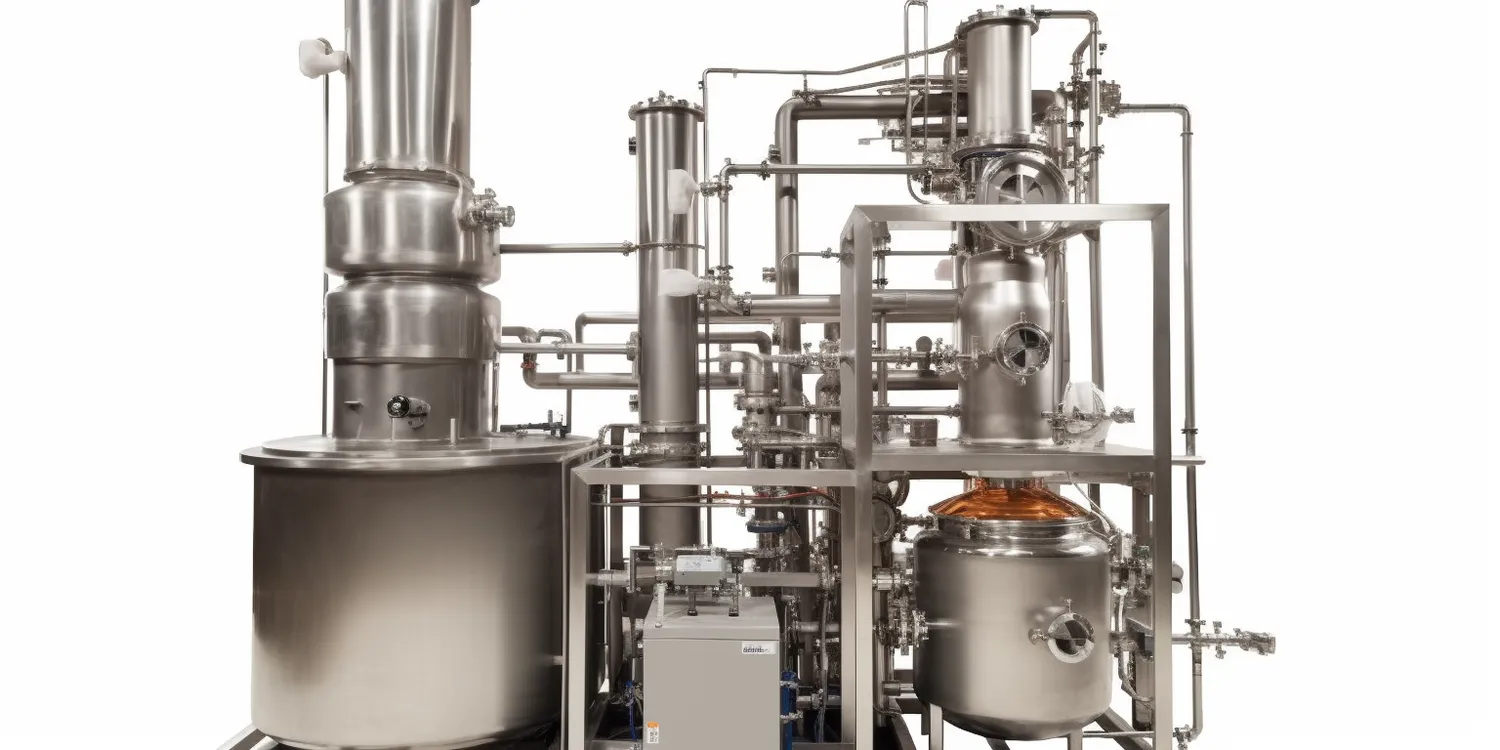
Stosowanie destylatorów przemysłowych wiąże się z wieloma korzyściami, które wpływają na efektywność i jakość produkcji. Przede wszystkim umożliwiają one uzyskanie wysokiej czystości produktów końcowych, co jest kluczowe w wielu branżach, takich jak farmaceutyka czy chemia. Dzięki zastosowaniu nowoczesnych technologii oraz automatyzacji procesów, destylatory te mogą pracować z dużą wydajnością i precyzją. Kolejną zaletą jest możliwość recyklingu surowców; wiele firm korzysta z systemów zamkniętych, które pozwalają na ponowne wykorzystanie rozpuszczalników czy innych substancji chemicznych. Dodatkowo nowoczesne destylatory są projektowane z myślą o minimalizacji zużycia energii oraz redukcji emisji szkodliwych substancji do atmosfery. To sprawia, że ich eksploatacja staje się bardziej ekologiczna i ekonomiczna.
Jakie wyzwania stoją przed użytkownikami destylatorów przemysłowych
Mimo licznych zalet stosowania destylatorów przemysłowych, istnieją również pewne wyzwania związane z ich użytkowaniem. Jednym z głównych problemów jest konieczność regularnej konserwacji oraz monitorowania stanu technicznego urządzeń. Wysoka temperatura oraz ciśnienie robocze mogą prowadzić do szybszego zużycia komponentów, co wymaga częstych przeglądów i ewentualnych napraw. Ponadto operatorzy muszą być odpowiednio przeszkoleni w zakresie obsługi tych skomplikowanych systemów, aby zapewnić ich bezpieczne i efektywne działanie. Innym wyzwaniem jest zarządzanie odpadami powstającymi podczas procesu destylacji; niektóre substancje mogą być toksyczne lub niebezpieczne dla środowiska, co wymaga odpowiednich procedur utylizacji. Również zmieniające się przepisy dotyczące ochrony środowiska mogą wpływać na sposób działania zakładów przemysłowych korzystających z destylacji.
Jakie są najnowsze technologie w destylacji przemysłowej
W ostatnich latach technologia destylacji przemysłowej uległa znacznym zmianom, co przyczyniło się do zwiększenia efektywności procesów oraz poprawy jakości uzyskiwanych produktów. Nowoczesne destylatory wykorzystują zaawansowane systemy automatyzacji, które pozwalają na precyzyjne kontrolowanie parametrów pracy, takich jak temperatura, ciśnienie czy przepływ. Dzięki zastosowaniu czujników i systemów monitorujących, operatorzy mogą na bieżąco śledzić przebieg procesu i wprowadzać korekty w czasie rzeczywistym. Wiele nowoczesnych destylatorów korzysta z technologii membranowej, która umożliwia separację substancji na poziomie molekularnym, co jest szczególnie przydatne w przypadku substancji o zbliżonych temperaturach wrzenia. Innowacyjne podejścia obejmują także zastosowanie destylacji z wykorzystaniem energii słonecznej czy geotermalnej, co przyczynia się do zmniejszenia zużycia tradycyjnych źródeł energii. Wprowadzenie sztucznej inteligencji do procesów destylacyjnych pozwala na optymalizację pracy urządzeń oraz przewidywanie awarii, co zwiększa bezpieczeństwo i niezawodność operacji.
Jakie są koszty związane z inwestycją w destylatory przemysłowe
Inwestycja w destylatory przemysłowe wiąże się z różnorodnymi kosztami, które należy uwzględnić przy planowaniu zakupu. Koszt zakupu samego urządzenia może być znaczny i zależy od jego typu oraz specyfikacji technicznych. Destylatory kolumnowe czy frakcyjne są zazwyczaj droższe od prostych systemów przepływowych ze względu na bardziej skomplikowaną konstrukcję oraz wyższą efektywność. Oprócz kosztu zakupu należy również uwzględnić wydatki związane z instalacją oraz uruchomieniem urządzenia, które mogą obejmować prace budowlane, elektryczne oraz hydrauliczne. Kolejnym istotnym aspektem są koszty eksploatacyjne, takie jak zużycie energii, wody czy surowców potrzebnych do procesu destylacji. Regularna konserwacja i serwisowanie urządzeń również generują dodatkowe wydatki, które należy brać pod uwagę w dłuższej perspektywie czasowej. Warto również pamiętać o potencjalnych kosztach związanych z przestrzeganiem przepisów dotyczących ochrony środowiska oraz bezpieczeństwa pracy, które mogą wymagać dodatkowych inwestycji w systemy filtracji czy monitorowania emisji.
Jakie są kluczowe czynniki wpływające na wybór destylatora przemysłowego
Wybór odpowiedniego destylatora przemysłowego to decyzja, która powinna być oparta na wielu kluczowych czynnikach. Przede wszystkim należy zwrócić uwagę na rodzaj substancji, które będą poddawane procesowi destylacji. Różne typy destylatorów są przystosowane do separacji różnych składników chemicznych; dlatego ważne jest dobranie urządzenia odpowiedniego do specyfiki produkcji. Kolejnym istotnym czynnikiem jest wydajność urządzenia; im wyższa wydajność, tym większe możliwości produkcyjne zakładu. Należy również rozważyć koszty eksploatacyjne oraz konserwacyjne związane z danym modelem destylatora. Warto także zwrócić uwagę na dostępność części zamiennych oraz wsparcia technicznego od producenta lub dostawcy sprzętu. W kontekście rosnącej świadomości ekologicznej przedsiębiorstw istotnym czynnikiem staje się również efektywność energetyczna urządzenia oraz jego wpływ na środowisko naturalne.
Jakie są przyszłe kierunki rozwoju technologii destylacji przemysłowej
Przemysłowa technologia destylacji znajduje się w ciągłym rozwoju, a przyszłość tego sektora zapowiada się obiecująco dzięki innowacjom technologicznym i rosnącemu naciskowi na zrównoważony rozwój. Jednym z głównych kierunków rozwoju jest integracja procesów destylacyjnych z odnawialnymi źródłami energii, co pozwoli na zmniejszenie śladu węglowego produkcji. Technologie takie jak destylacja solarna czy wykorzystanie energii geotermalnej stają się coraz bardziej popularne i mogą znacząco wpłynąć na efektywność energetyczną zakładów przemysłowych. Ponadto rozwój sztucznej inteligencji i analizy danych otwiera nowe możliwości optymalizacji procesów produkcyjnych; dzięki algorytmom uczenia maszynowego możliwe będzie przewidywanie awarii oraz automatyczne dostosowywanie parametrów pracy urządzeń do zmieniających się warunków. W kontekście rosnącej konkurencji na rynku kluczowe stanie się także poszukiwanie nowych metod separacji substancji chemicznych, które będą bardziej efektywne i mniej energochłonne niż tradycyjne metody destylacji.
Jakie są najlepsze praktyki dotyczące obsługi i konserwacji destylatorów przemysłowych
Aby zapewnić długotrwałą i efektywną pracę destylatorów przemysłowych, niezwykle istotne jest przestrzeganie najlepszych praktyk dotyczących ich obsługi i konserwacji. Regularne przeglądy techniczne powinny być przeprowadzane zgodnie z zaleceniami producenta; obejmują one kontrolę stanu komponentów mechanicznych oraz elektronicznych urządzenia. Ważnym aspektem jest również czyszczenie systemu; nagromadzenie osadów może prowadzić do obniżenia wydajności oraz jakości produktów końcowych. Operatorzy powinni być odpowiednio przeszkoleni w zakresie obsługi urządzeń oraz procedur awaryjnych; znajomość zasad BHP jest kluczowa dla zapewnienia bezpieczeństwa pracy w zakładzie przemysłowym. Dobrze jest także prowadzić dokumentację wszystkich działań konserwacyjnych oraz naprawczych; pozwoli to na łatwiejsze identyfikowanie problemów oraz planowanie przyszłych działań serwisowych.
Jakie są różnice między małymi a dużymi destylatorami przemysłowymi
Różnice między małymi a dużymi destylatorami przemysłowymi są znaczące i mają wpływ na ich zastosowanie oraz efektywność produkcji. Małe destylatory często stosowane są w laboratoriach lub małych zakładach rzemieślniczych; charakteryzują się prostszą konstrukcją i mniejszą wydajnością, co sprawia, że są idealne do eksperymentów lub produkcji niewielkich ilości substancji chemicznych. Z kolei duże destylatory przemysłowe przeznaczone są do masowej produkcji i charakteryzują się bardziej skomplikowaną budową oraz zaawansowanymi systemami automatyzacji. Dzięki większej powierzchni wymiany ciepła oraz zastosowaniu kolumn frakcyjnych, duże jednostki potrafią osiągać znacznie wyższą wydajność i jakość produktów końcowych. Koszty inwestycji w duże destylatory są oczywiście wyższe, jednak ich eksploatacja może być bardziej opłacalna w dłuższej perspektywie czasowej ze względu na niższe koszty jednostkowe produkcji.